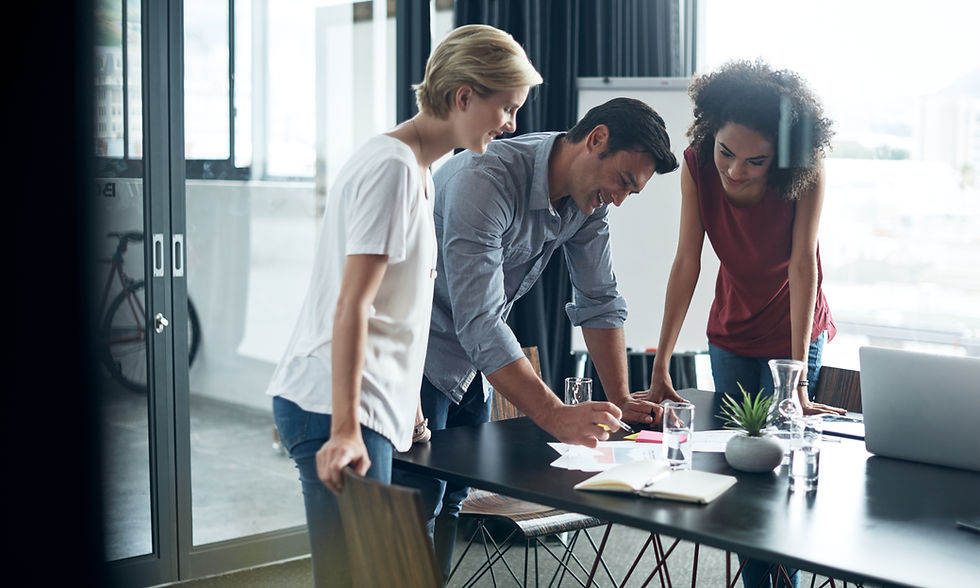
WELCOME TO HOLISTIC LEAN ENTREPRISE
DR GARCIA PATRICK
ABOUT US
Holistic Lean Entreprise (HLE) Dr Garcia Patrick offers the comprehensive capabilities and deep industry knowledge, expertise and experience necessary to help you solve the most complex issues of your organization, especially the improvement of your major business processes and the lead to your digital transformation.
HLE has been founded in 2017 by Dr Patrick Garcia who made a international career of researcher, university teacher and industry director in the aeronautics and automotive activities.
Since its creation HLE has been very active in the Industry worldwide, especially in the automotive and education fields.
Want to experience the expertise of Holistic Lean Entreprise Dr Garcia Patrick for yourself? Give us a call today and let’s discuss what we can do for you.

YOUR BENEFITS. THE VALUE PROPOSITION.
Hard Benefits. Productivity Improvement.
Shorter time to Market. 20 to 60%.
Lead-time Reduction of Products and Services Development. 20 to 80%.
Efficiency Increase of Engineering and Administration Services in terms of Cost, Time and Quality. 2 to 10% per year.
Exchange of Best Practises within the Organization. 2 to 5% productivity per year.
Developing a more consistent problem-solving mindset (Seeing Waste,Finding Root Causes, Continuous Improvement). 2 to 5% per year.
The foundation for a strong digital transformation.
Soft Benefits.
Win Win situation between Employer and Employees.
Improved communication and alignment between departments
Increased moral and motivation of the employees.
Enhancement of a strong culture.


LEAN MANAGEMENT APPLIED TO PRODUCT AND SERVICE DEVELOPMENT
Methodology based guidance to solve your problems related to your organisation. Holistic approach to address cross functional process improvement. Top down and bottom up strategy and implementation of Change Agent to sustain your lean management system.
With years of experience, our staff has the capabilities and expertise to take your business to the next level. At Holistic Lean Entreprise Dr Garcia Patrick, we combine our insights and skills to transform your processes and strategies, and in turn, your company. We’re proud to help shape and improve how our clients structure and manage their business.
TRAINING AND EDUCATION PROGRAMS
Education training to get your people familiar with Lean Management and gives them the ability to apply the lean principles to their daily business.
Several training modules are designed to allow the trainees to efficiently execute the workshops (defined during the planning phase) which take place just after the training. The trainees are not only engineers but administrative employees like HR, Finance, Sales, Logistics,... and operation people. These training modules are articulated around the simulation of product, service and manufacturing processes. They are illustrated by some practical industry and service cases analysis.


INTERNAL PROCESS AUDIT
Assessment of the business processes including Gap Analysis and Implementation Plan.
This audit consists of interviewing your key players and analyzing some key data in order to identify the strengths and weaknesses of your major business processes. The evaluation is executed according to a well structured score matrix to show the opportunities and risks.
AGILE DIGITAL TRANSFORMATION.
Expert Guidance
Looking to develop your digital transformation but not sure where to turn? Need help planning, or executing your next steps? Let us guide you. Any organization can move forward with small incremental changes, but building for the future in today’s rapidly evolving environment means taking bold chances and making insightful decisions. Business models, entreprise organization including major business processes need to be reconsidered and updated to face the rapid rise of digital technologies. Agile lean management applied to product and service development transform process, people and organization to thrive in the digital age! Digital transformation and lean management are the two faces of the same medal ! It is not about technologies but it is about a mindset to create value to your company and yours customers. Digital and agile lean transformations require a holistic approach getting rid of the silos existing in a traditional enterprise. To start your transformation you need a strong agile methodology to rapidly align your organization and to efficiently drive your effort to tangible benefits.
OUR TESTIMONIALS DO THE TALKING
Our Reputation Speaks for Itself
There are few things as rewarding as a successful collaboration that solves a challenge. Our team of professional business consultants use their years of experience and knowledge to create lasting and rewarding relationships with our business partners. Check out what our clients are saying about working with Holistic Lean Entreprise Dr Garcia Patrick.
When we decided to work on our Engineering processes with Aptiv two years ago, we chose to work with Patrick and he had a huge impact on our efficiency improvement. He managed to help identifying the key waste sources in our processes, mobilized our Engineering community in a pragmatic and agile way, and then supported the efficiency program by coaching our team across all Europe with his experience and his methodology. This has been a great journey thanks to him !
Jean-Noël Truchet. Transformation leader | Operations & Turnaround seasoned manager | P&L improver | Process and Assembly industries at Aptiv.
Patrick is a strong driving force in implementing a necessary change management culture and implementing lean processes. His rich knowledge in Lean became invaluable when setting up a development centre in Poland. By educating and empowering the people, simple solutions were found for complex problems. Even in difficult economic, cultural and political boundaries, Patrick is result driven, leading the team to impressive results. Working with Patrick over several years was a continuous professional learning and developmental process for me, for which I’m grateful.”
Dr. Jan-Friedrich Brand
Director – R&D
Sharda Motor Industries Ltd.
Patrick Garcia has been studying and practicing Lean Product Development principles for over a decade.
His first pilot projects as Engineering Manager at Tenneco showed tremendous results.
Over his time at Tenneco, he then led the lean transformation of product development and transactional processes in Europe. His ability to not only teach lean techniques but engage disparate teams to collaborate together to solve local and enterprise-level problems is a credit to his facilitation skills.
We have collaborated on several papers that documented his successes while at Tenneco and have been presented at past Society of Automotive Engineering congresses.
Patrick is a solid practitioner, a great teacher and a thoughtful coach
John Drogosz. V.P. Lean Services at Liker Lean Advisors
Patrick played a very important role in Tenneco while we both worked there in transforming engineering product development processes to be much leaner, quicker, and more efficient. He was also able to improve other administrative processes in various functional areas when he shifted his focus from engineering product development to the application of lean processes in general. He would be a good person to introduce lean principles and help in implementing them in organisations.
Abhijit Mukherjee.
Managing Director at AM Collogue. Belgium
Patrick is an outstanding leader in helping organizations adapt lean principles to business processes; essentially "beyond the shop floor". I have worked directly with him as he helped our team layout basis for business mapping that would eventually become the foundation for a CRM. I appreciate his work ethic and knowledge, and I have successfully used the information and techniques Patrick has shared to drive efficiency in processes within both product management and marketing.
Annette Chantaca. HFI Detroit. Director, Product Management, Marketing and Communications
We met with Patrick in Germany, Edenkoben, both working @ Tenneco Automotive. I have been amazed by his ability to work in team driving change and efficiency, focusing on innovation, organization and people development.
Jean François Barth. Managing Partner at PERIT Consulting. Belgium.
I’ve been working with Patrick when I was at APTIV since we started wondering about engineering efficiency and resource allocation. His background in the industry, his experience and methodology in the lean management were a great support to support and coach our team in a very efficient way: he pushed us to focus on the business relevant targets and, thanks to his good understanding of the company organization, identify key stakeholders and major intermediate milestones to get required executives approval and support. I’ve much appreciated his capability to quickly understand the complex business challenges we were facing and his personal involvement all along the project to deliver the results as expected.
Nicolas Chauland. Safran Seat Division.
Patrick Garcia had a leadership role within Tenneco as director of acoustics and advanced engineering during the time I worked with him there. As leader of the global Ford business unit and then Vice President of the Commercial Vehicle and specialty systems business unit, we engaged Patrick often to provide his vast knowledge and skill sets to help us achieve strict decibel levels, sound tuning, and NVH improvements. Patrick helped us to achieve targets on vehicle classes from A to heavy truck and off road vehicles as well. His work on complex vehicle systems, which often included multiple engine configurations, hence a wide variety of harmonics, and body types, building complexity in mounting and vibration transmission, allowed us to satisfy our customer demands and needs and allowing them to meet varying global vehicle restrictions. And helping assure we were profitable in our efforts. Great team player.
Lois Boyd. Retired, Former President Hertz Equipment Rentals, currently mentoring and volunteering.
Patrick has developed reliable and proven skills as a transformation consultant . On many occasions, notably in transaction services he has demonstrated pervasive and determined leadership skills. His approach is highly structured in identifying, planning and executing transformation projects while delivering measurable benefits. If you realise the necessity to evolve your organisation to be more competitive and take on a transformation program, Patrick's contribution would be a key enabler to success.
John Mikael Charlton. Former VP at Tenneco.
Patrick and I worked together from 2002 to 2008 at Tenneco. In his responsibilities as head of Engineering and Lean, Patrick was one of the key persons at the center of the decision-making processes. His capacity to impulse changes, particularly in terms of product innovation and Lean transformation made a great difference. None of the projects that my team was awarded would have been successful without Patrick and his department. When I took over sales and programs in China, Patrick support continued to play a major role in the development of a state-of-the-art R&D center: training of Chinese engineers in Europe, transfer of technologies. His department in Europe was the reference within Tenneco’s global organization: not only a center of competence but also of excellence. I particularly remember the decisive competitiveness advantages brought by new acoustic simulation and multiaxial durability testing and simulation systems. These tools were developed by Patrick’s team and were the product of a true understanding of what is innovation and what is Lean in engineering. Even so our carriers moved in different directions, I will have no hesitation to work with Patrick again. If you intend to transform your company I strongly recommend Patrick as a passionate and highly efficient leader.
Paul Labic. Risk management, anti-corruption and compliance advisory at PBL Management.
When it is about an agile transformation (lean or digital) of your Enterprise I strongly recommend you Patrick for his ability to set up and convert the transformation in tangible benefits for your company. As VP and General Manager of the European division of Tenneco Ride Control , I worked several years together with Patrick, as Transformation leader , to further improve the efficiency of the product development, Sales, Human Resources and Logistics. We started the long journey by establishing the mission in order to get the buy in of the full organisation , a strategy based on a combined smart Top Down and Bottom Up approach to make the transformation sustainable, and a road map supported by a strong agile methodology to deliver the tangible benefits. During this transformation process the progresses and the results were amazing! Our efficiency in Engineering, Sales, HR and Logistics were strongly improved and allowed us to do much more with the same amount of resources! The return on the money invested during the consultancy projects was largely positive. The collaborative way of working between the different functions was deeply enhanced. Furthermore the employees showed a lot of enthusiasm to modify/ improve their environment and consequently they were highly motivated and engaged to support the transformation ! A lot of stunning stories that you can investigate in more details in the SAE papers attached on this site!
Sandro Paparelli. Former VP in charge of the European Ride Control Division at Tenneco.
Great professional. Patrick helped us to increase efficiency in our complex (multi locations and cultures) engineering organization with great results and impact.
Jean Laurent Donato Senior VP/ Directeur Général. Groupe Aries Alliance.

CONTACT SUPPORT
How Can We Help?
HOLISTIC LEAN ENTERPRISE
The founder
SHOW CASES. PUBLICATION FILES.
In this file list You will find the lean management experience collected during the 20 last years. This list starts with lean management introduced in engineering and then extended to Finance, Sales and HR. The creation of a new R&D center gave the opportunity to implement lean management from scratch. The lean management strategy and its execution are explained and illustrated with detailed cases.
1. LEAN MANAGEMENT APPLIED TO ENGINEERING. FIRST IMPLEMENTATION IN A MAJOR AUTOMOTIVE SUPPLIER.
Lean management applied to product and service development is the key enabler to a strong lean production system. Lean engineering affects many organizations within the entreprise including purchasing, sales, finance, human resources and manufacturing. Three fundamental elements must be integrated to create a high performance lean engineering
- high skilled people
- powerful tools and technologies
- strong processes.
This paper illustrates some selected cases regarding typical engineering activities like
- Computed Aided Design
-Computed Aided Engineering
- Testing
- and standardization of component design
For the concerned company it was the start of a long journey with lean management.
Keywords. Lean methodology. Current and future value stream maps. Gap analysis. Metrics. Product development cycle. Kentou or concept phase. Set based engineering. Trade off curves. CAE and CAE simulation tools. Engineering checklist. Product development and design guidelines. Convergent versus iterative model. Process value stream map. Component standardization. Knowledge based manufacturing and engineering. Lessons learned. Visual management. Cockpit. Obeya / war room.Benchmark displays.
2. LEAN MANAGEMENT APPLIED TO ADMINISTRATIVE ACTIVITIES. FINANCE.
Lean management can be applied to administrative processes. These cases are referring to Finance function which is playing a central role in several major business processes of an entreprise.
Some different cases are illustrated like improved cash flow, better invest approval and execution processes, customer request for quotation.
The workshops generated some high process lead-time reduction up to 70% and some considerable cash flow improvement.
Keywords. Lean methodology applied to transactional / administrative processes. Current and future value stream maps. Gap analysis. Metrics. Tooling lead-time reduction. Request for quotation. Costing. Cost break down. Lean passing invest into usage. Lean management of the account receivable and payable. Poka Yoke applied to finance. Hard and soft benefits. Lessons learned.
3. LEAN MANAGEMENT APPLIED TO HUMAN RESOURCES.
This paper illustrates some examples of improved processes related to Human Resources. It includes
- the “on-board” or integration process
- the management of employee flextime accounts
- process to create and manage some critical certificates in a short time window
- absenteeism reduction in one company plant
Keywords. Lean cross functional methodology. Current and future value stream maps. Gap analysis. Metrics Identification and Hiring Processes. On board Processes. Inverse T Model. Skills matrix. Personnel Flexibility. Retention Strategy. Current and future value stream maps. Metrics. New HR standards. Absenteeism reduction.
4. LEAN TRAINING MODULES.
The training module consists of simulating
- a traditional product development process. This simulation demonstrates the typical wastes the development team is experiencing in its daily business!.
- an improved process by integrating stepwise the lean principles.
Finally the students analyze the impact a lean system on the Customer, Employer and Employees.
Keywords. Customer expectations. Traditional product development process. Types of wastes. Concept or Kentou phase. Kanban. Problem solving, PDCA and 8D tools. Value stream map. Gap analysis. Metrics. Concurrent engineering. Trade off curves. Design guidelines. Set based engineering. Percent loading chart
5. APPLICATION OF LEAN MANAGEMENT TO A NEW R&D CENTER CREATED DURING AN ECONOMICAL CRISIS.
These 2 papers illustrate how efficient the application of lean principles can boost the development of a new R&D center. The lean journey starts with a white paper including a vision and objectives in order to align the organization.
This new center was built on 3 major pillars
-Robust processes
-High skilled and motivated people
-Appropriate tools and technologies to support the processes and people.
Facing a severe downturn the new R&D center had to adjust itself to the limited resources and budget. Innovation and creativity were the key enablers to overcome this very challenging situation.
Key words. White paper. People hiring,training and retention. Alignment strategy, Hoshin Kanri. Engineering work cell organization. Integration of partners. Process value stream map. Front loading. Set based engineering. Parts standardization. Soft tools, visual management, problem solving 8D, Plan Do Check and Act. Product guidelines as outputs of lessons learned. Hardtool, Knowledge Based Manufacturing and Engineering.
Part 1.
5. APPLICATION OF LEAN MANAGEMENT TO A NEW R&D CENTER CREATED DURING AN ECONOMICAL CRISIS.
File Body
6. HOW TO SPREAD THE LEAN MINDSET IN AN EFFECTIVE WAY USING CHANGE AGENTS IN SALES AND ENGINEERING AND FINANCE.
In the implemention of lean management the probably most challenging phase is to sustain the lean system within an organization as part of a philosophy of continuous improvement. During the early years of implementation, lean was managed as a top down approach which consisted of identifying, executing, and tracking lean projects by the management, a small number of people and lean experts.
This approach had the advantage of building up critical mass and helped to instill a lean change culture in a reasonable timeframe. But the experience showed that even if early results were encouraging, the implementation was not consistent enough to sustain a mindset of continuous improvement.
This top down approach needed to be reinforced by a much stronger bottom up approach which consisted of group leaders acting as change agents. Their roles and responsibilities included designing processes and standards ,problem solving, teaching their people and sharing the knowledge captured.
This paper describes the lessons learnt by lean change agents in Sales, Engineering and Finance departments at a major automotive supplier.
Keywords. Lean management. Continuous improvement. Change agents. Structure of lean workshop. Standards. Problem solving. Teaching. Knowledge capture. Buttom up. Top down. Lean leadership vs traditional leadership. Mentoring. Coaching. Company culture. Change agent profile. Win win benefit for the company and employees. Lean workflow.
7. LEAN MANAGEMENT APPLIED TO ADVANCE ENGINEERING AND PRODUCT DEVELOPMENT.
Illustration of some Lean engineering principles. SAE paper.
These papers illustrate some key lean management principles applied to advance engineering and product development
-Establish customer based value
-Front loading to thoroughly explore alternative solutions while there is a maximum design space.
-Visual management.
Keywords. Kentou or concept phase. Set based engineering. Trade off curves. CAE and CAE simulation tools. Engineering checklist. Product development and design guidelines. Convergent versus iterative model. Component standardization. Knowledge based manufacturing and engineering. Lessons learned. Cockpit. Obeya / war room.Benchmark displays.
8. IMPLEMENTATION OF A NEW LEAN INNOVATION STRATEGY .
Lean management applied to some innovation processes. SAE paper.
A good innovation process is the key for the future success and ongoing well being of a company.
In this paper a methodology was developed to analyze the market, current and future customer demands and to monitor the competition. From these analyses the trends and new technologies were derived to meet the requirements.
Keywords. Innovation strategy. Project control. Project development cycle. Technology road map. Innovation drivers. Process of innovation. Generation of ideas. Rating process. Application of 2 innovation complimentary approaches WOIS and Strategos. Business case. Concurrent engineering. Project review.
9. LEAN KBME (KNOWLEDGE BASED MANUFACTURING AND ENGINEERING) PROCESS AND TOOL.
The KBM&E Process and tool can be defined as an intelligent CAD System. It has the power to collect all the lessons learned during the product development projects and dedicated lean workshops. This product knowledge is formulized in form of design and manufacturing guidelines which are mapped in the CAD Modeling.
The benefits are
- to sustain the knowledge capture in an agile way compared to knowledge data base.
- to improve the alignment of Engineering and Manufacturing
- to optimize the product development cycle by reducing the time to market.
- to relieve the designers / engineers from mundane tasks
-to free up more time for innovation.
Keywords. Lean engineering. 6 Sigma. PLM system. Knowledge capture. Lessons learned. Intelligent CAD / CAM systems. Part standardization. Parametric engineering. Constraint based systems. Shorter time to market. Component/subsystem templates. CAE simulation tools.
10. FIVE LEAN PRINCIPLES APPLIED TO PRODUCT AND SERVICE DEVELOPMENT.
According to Womack and Johns the 5 lean principles are applied to Product Development
- specify Customer Value
- identify the Value Stream of a service
- make flow.
- let the Customer pull the service from the service provider instead of pushing it.
- strive for perfection
Keywords. Customer values. Value stream analysis. Flow Pull vs Push. Continuous improvement. Problem solving methods. Concept phase. Trade Off curves. Set Based Engineering. Standardization. Lean soft vs hard tools.
11. LEAN ENGINEERING. BEST PRACTICES.
This paper explains and illustrates some best practises according to 2 lean principles
- establish customer-defined value
- Front-load to thoroughly explore alternative solutions while there is maximum design space. Kentou (study) phase with set-based concurrent engineering.
Keywords. Customer value. Concept or Kentou phase. Trade off curves. Set Based Engineering. Concurrent Engineering. Product development cycle. Funnel strategy. Mid up standardization.
12. IMPLEMENTATION OF LEAN TRANSACTIONAL. PART 1. START OF A LONG JOURNEY.
Illustration of lean management in the administrative area. SAE paper.
After more than one year of lean transactional implementation, the results were very encouraging
- Significant reduction of cross-functional process lead times
from 20% to more than 50%.
- Freed-up time (less effort) due to waste elimination. Redeployment of the freed-up time to high value-added tasks.
- improved quality and accuracy of data reports
- improved communication and alignment between
departments
- improved cross-functional team building
- a more consistent problem-solving mindset.
- significant improvement in motivation and morale
Keywords. Lean transactional or administrative. Implementation phase. Finance. Cross functional business processes. Value stream map. Gap analysis. Current and future state maps. Metrics. Lean transactional principles guidelines. Lean workflow.
13. IMPLEMENTATION OF LEAN TRANSACTIONAL. PART 2. LESSONS LEARNED.
After a couple of years of implementation the lean methodology was reviewed and improved in order to deliver the expected results in a more efficient way.
Some first lean experience showed that project execution took too much time, resulting in the risk of demotivating
people and reducing the credibility of the company lean strategy. An experienced team from finance and sales & engineering worked to understand the root causes and find a
new way of:
- identifying
- preparing
- executing
- tracking
- and closing the lean projects in a more efficient way.
Keywords. Lean methodology efficiency. Lean projets and workshops. Lessons learned. Gaps and roots causes analysis. Correction plan. Methology guideline. RASIC (Responsable, Active, Support, Informed Communication).
14. LEAN MANAGEMENT STRATEGY. SELF LEARNING ORGANISATION.
The different implementation steps described in this paper are required to reach the critical mass and maturity to lead the organization toward a self learning organization.
The cornerstone of this transformation is to implement and live the contnuous improvement (Continuous Improvement Cycle or CIC). The outcome of the CIC are threefold;
- improve the processes
- develop the people skills
- increase the knowledge of the organization
The Continuous Improvement Cycle was fully integrated in the daily business in order to ensure a good knowledge capture and sharing.
Keywords. Lean management strategy. self learning organization. Continuous improvement. Top Down and Bottom Up strategy. Problem solver. Lean teacher. Knowledge capture and sharing. PDCA/Plan Do Check and Act. Change Agent. Lean Management sustainability. Mechanistically or organically managed systems. Enabling bureaucracy. Role of the Lean Sensei. Product development vs transactional training modules. Lean virtuous circle. Cases.